Overview of the initiatives implemented this year
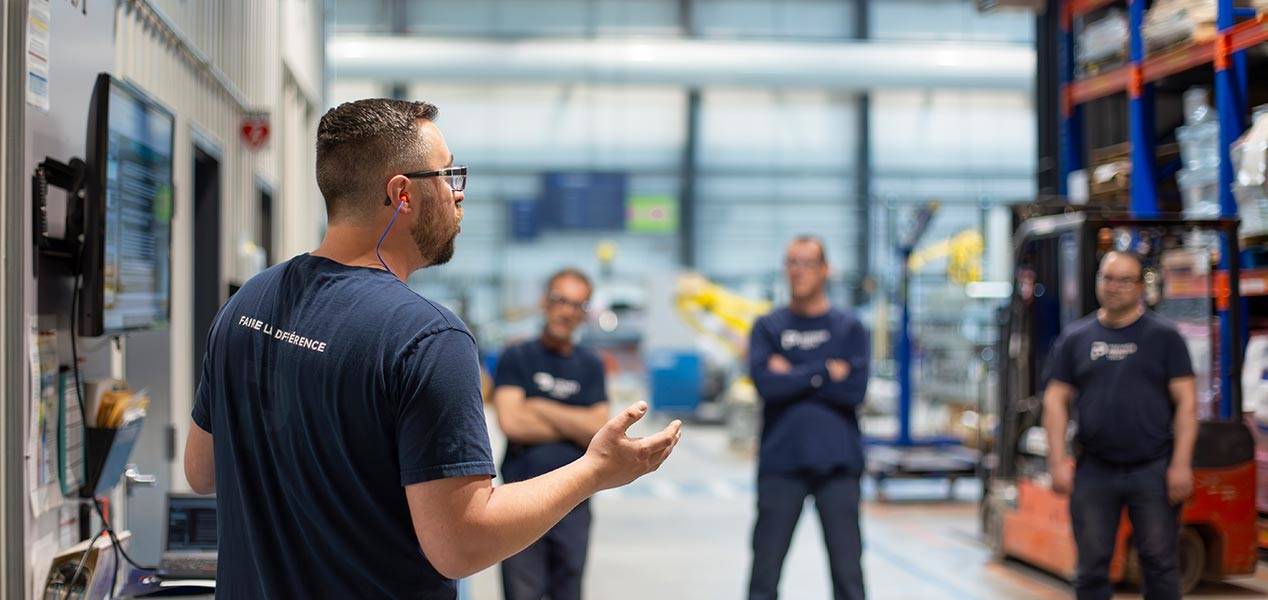
As part of the continuous improvement of our business and production practices, we are committed to reducing our footprint, including our GHG emissions and the management of raw and residual materials.
This commitment fostered collective engagement and raised awareness of ecoresponsibility, leading to the launch of many initiatives across our home bases throughout the year.
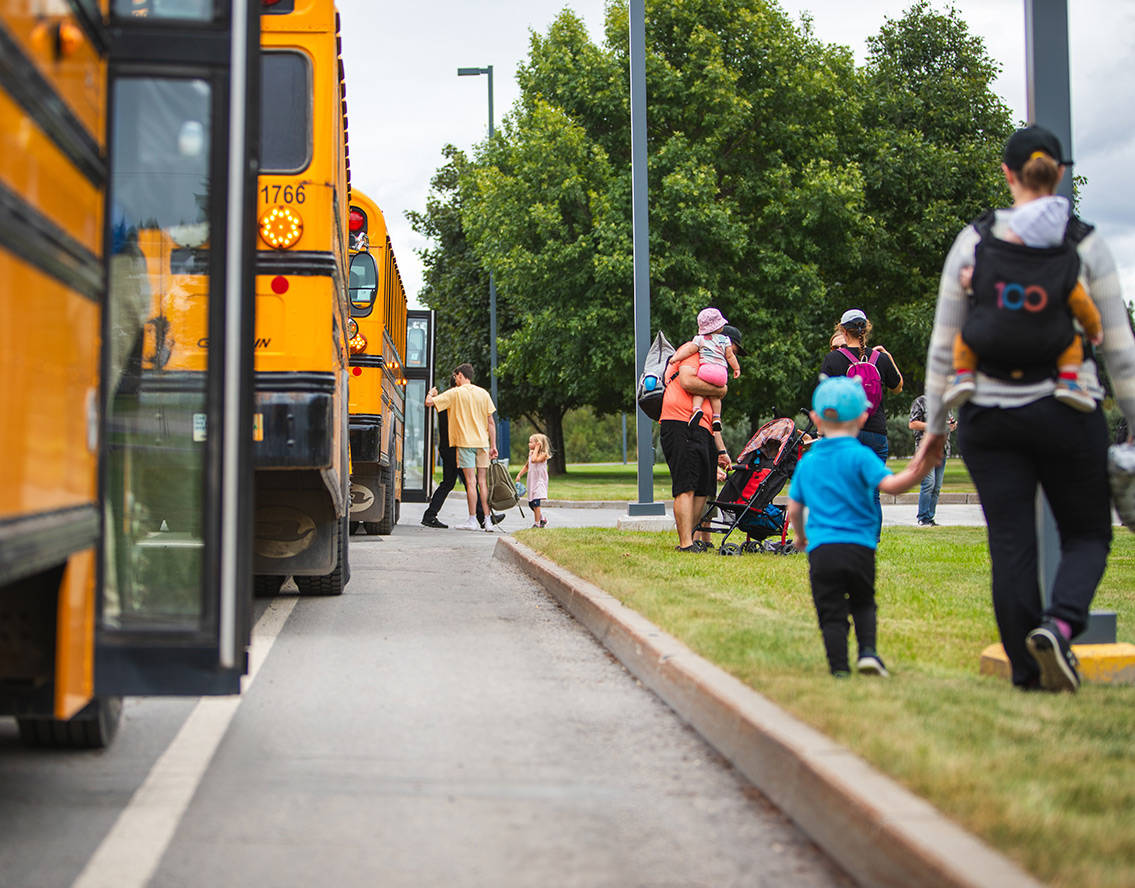
Ecoresponsible practices at events
The 100th anniversary celebrations on the Premier
Impactful IR&D actions
Premier
To support the group’s partners in wastewater treatment maintenance services and address the challenges they face — the significant growth of activities and the labour shortage in the North American market —, the Innovation, Research and Development (IR&D) team focused its efforts on finding solutions. The team conducted a service offer analysis for standard industrial equipment — the vacuum truck —, which highlighted energy waste. So, an innovative solution was found through the integration of a new aspiration method using an air compressor. This compact, efficient and easy-to-transport solution represents a significant cost saving for our service partners and optimizes their operations. It also cuts diesel consumption by approximately 32%, thus mitigating the environmental footprint of service operations.
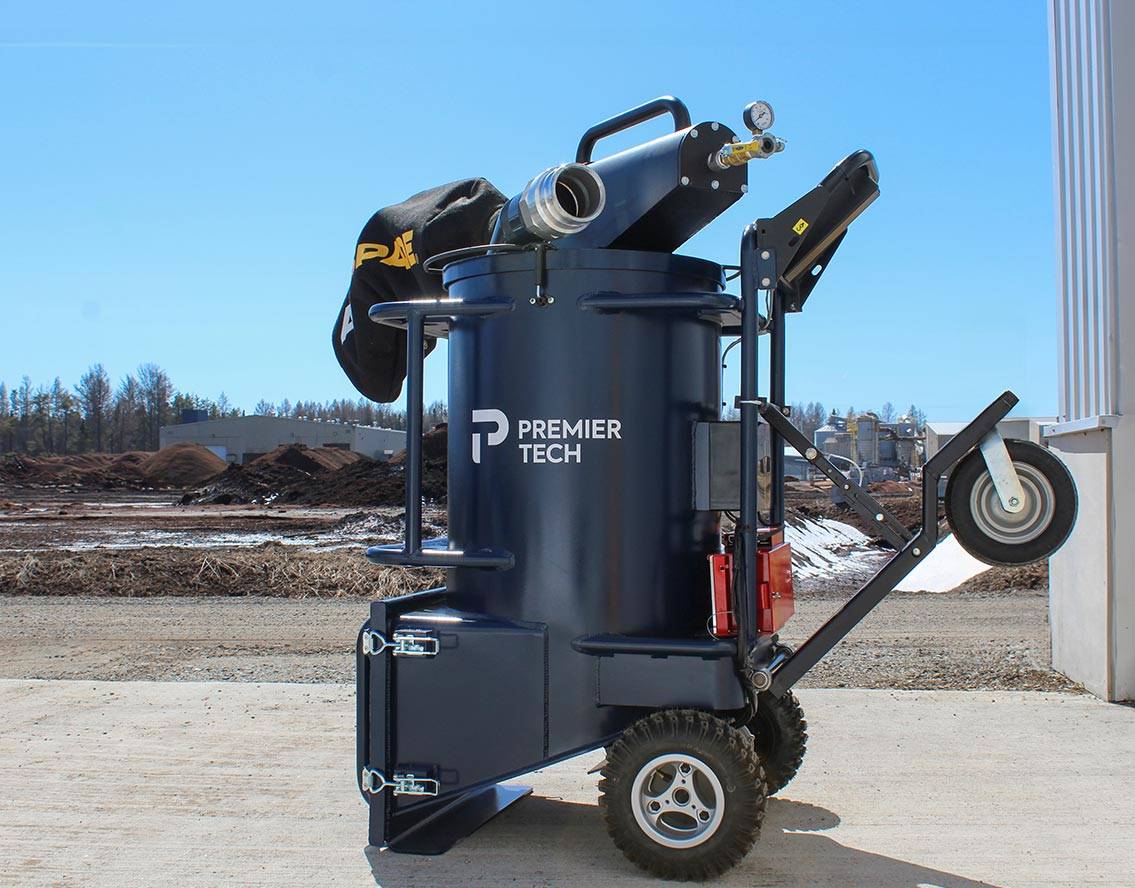

Integration of new ecoresponsible practices
Premier
This year, the business group has integrated a new aspect to its well-established active management process, which aims to cover various subjects such as health and safety, productivity improvement or any other improvement opportunities identified by manufacturing teams.
Environmental initiatives are now fully part of these weekly meetings, allowing everyone to suggest environmental improvements.
A plastic circularity pilot project
Premier
A plastic recycling pilot project has been implemented in collaboration with Modix Plastique, a high-quality post-consumer resins recycling and manufacturing company, and PolyExpert, a polyethylene film manufacturer. This initiative has a three-step circular economy target: recycling bags from mega bales packaging used for inter-site transports, transforming these bags into post-consumer reprocessed resins, and integrating these resins into a plastic film used for the production of new growing media bags.
This pilot project allowed the plant in Rivière-du-Loup to recycle over 45 tons of plastic this year.
Introduction of recycled plastic material
Premier
Among its ecoresponsible production practices, the business group has introduced recycled plastic material (RPM) into its products. This commitment to reducing the utilization of virgin resins and offering more ecoresponsible products takes two forms: the introduction of recycled polyethylene in the rotomolded products and the purchase of recycled plastic parts. For example, all the PVC tubes used in our solutions are now made from recycled PVC.
In 2023, our business unit in France received the MORE label — MObilised for REcycling — from Polyvia, the Federation of Plastics Processing and Composites. This label recognizes the integration of post-consumer waste and post-industrial RPM, demonstrating the best practices that have been implemented in this regard.
Energy savings
Premier Tech Water and Environment
To enhance energy efficiency and reliability of compressed air generation equipment, our team in Châteauneuf-d’Ille-et-Vilaine, France, replaced three air compressors that had reached the end of their life cycle by two 15
*This story is from the Premier Tech Report 2024.
Read the complete 2024 sustainability report
As we embark on our second century of history, we reflect on a year fuelled by our potential to create a lasting, positive impact. Learn more about actionable initiatives we implemented over the past year, driven by sustainability and beyond.